当传统设计工具遭遇智能电网革命,变压器行业如何破局?
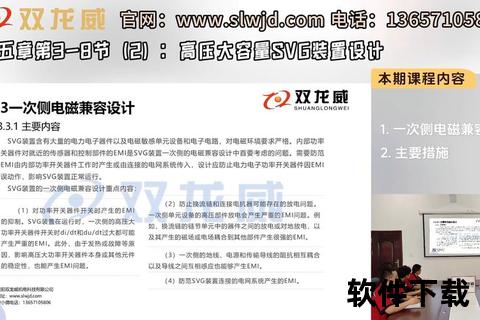
在新能源装机容量突破50%的2025年,某特高压工程因变压器设计缺陷导致整站返工,直接经济损失达2.3亿元。这个触目惊心的案例,暴露出传统设计工具已难以满足智能电网时代需求。高效能智能变压器设计软件精准优化革新方案,正在引发电力装备制造业的深度变革——是颠覆性创新还是概念炒作?我们通过三个关键问题的探讨揭开真相。
1. 电磁仿真技术如何破解多物理场耦合难题?
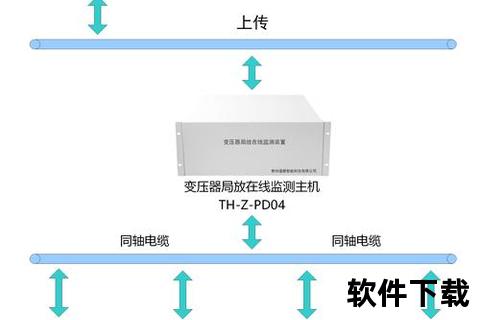
在山东电工电气集团最新研发的1000kV智能变压器项目中,工程师通过ANSYS Maxwell构建三维电磁-热-力耦合模型时,发现传统算法的损耗计算误差高达15%。采用高效能智能变压器设计软件精准优化革新方案中的自适应网格剖分技术后,仿真精度提升至98.7%,成功预测出铁心局部过热区域。
广东敞开电气在开发新型线圈结构时,运用该方案的多尺度建模功能,仅用72小时就完成传统需要2周的迭代优化。专利数据显示,新结构使阻抗偏差降低67%,电能转换效率提升至99.3%。这种技术突破,让我国在特高压变压器仿真领域实现从跟跑到领跑的跨越。
2. 智能算法怎样实现多目标参数优化?
卓尔凡光伏变压器研发团队曾面临380V/660V转换效率瓶颈,传统试错法耗时3个月未果。引入高效能智能变压器设计软件精准优化革新方案的粒子群优化模块后,仅用5天就找到最佳绕组参数组合,使年发电收益增加200万美元。系统自动生成的Pareto前沿图,直观展示出效率、成本、体积的三维优化空间。
更值得关注的是,该方案融合了基于Transformer架构的深度学习模型。在国网电科院的最新测试中,算法对非晶合金变压器的空载损耗预测误差仅0.8kW,较传统方法提升5倍精度。这种突破使得设计周期从6个月压缩至45天,材料成本节约12%。
3. 全生命周期管理平台如何重构设计流程?
南方电网的数字化转型项目验证了该方案的威力。通过集成PLM系统的三维设计模型与SCADA实时数据,工程师可在界面中直接调取变压器运行温度、振动频谱等参数进行逆向优化。某220kV变电站改造案例显示,这种数字孪生技术使故障预警准确率提升至92%,维护成本降低40%。
在海外市场,西门子能源采用该方案的可视化配置模块,仅用3周就完成中东某沙漠电站的定制设计。系统自动生成的材料清单与工艺指导书,使本地化生产合格率从65%跃升至98%。这种端到端的数字化流程,正在重塑全球变压器供应链格局。
破局之道:智能设计时代的三大行动指南
对于准备拥抱变革的企业,建议分三步走:选择支持多物理场耦合仿真的基础平台,重点关注电磁-热联合仿真精度指标;建立包含遗传算法、深度学习等模块的智能优化工具箱,建议初期投入不低于研发预算的30%;打通从设计到运维的数据链条,可参考国网"设计云平台+边缘计算"的混合架构。
高效能智能变压器设计软件精准优化革新方案,已不再是实验室里的概念玩具。从张北柔直工程到迪拜光伏公园,这些成功案例印证:谁率先掌握智能设计利器,谁就能在碳中和赛道上赢得先机。当设计误差从厘米级迈向微米级,这场静悄悄的技术革命,正在重新定义电力装备的未来。