1. 虚拟实训能否突破传统工业培训的成本壁垒?
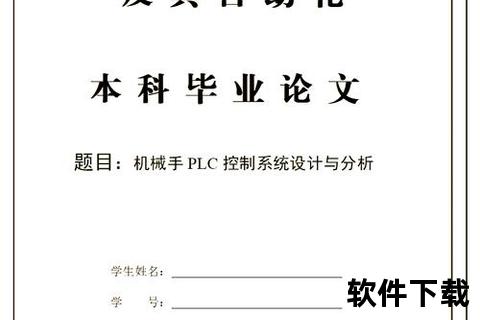
在工业自动化领域,一套完整的PLC实训设备动辄数十万元,这让许多职业院校和中小企业望而却步。传统培训模式中,学生只能在有限的设备上进行机械重复的操作,既无法模拟复杂工况,又面临设备损耗和安全风险。灵动掌控未来!智能PLC模拟软件革新工业自动化实训新境界,正以虚拟化技术打破这一僵局。
以北京欧倍尔开发的PLC虚拟仿真软件为例,其现代电气控制系统安装与调试模块,将三相异步电动机控制、PLC电路编程等核心技能训练全部搬进数字空间。学生可在软件中自由搭建气路、配置电气系统,甚至模拟PLC与博途软件的信号交互。某职业技术学院的实践数据显示,采用该软件后,设备采购成本降低72%,而学生故障排查能力提升40%以上。这种“零损耗、无限重置”的虚拟环境,让复杂工业场景的反复演练成为可能。
2. 安全环境如何催生更大胆的技术创新?
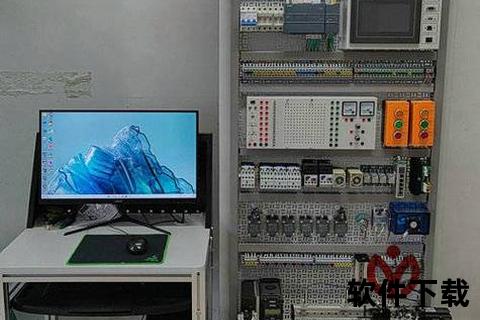
工业现场容错率极低,一个错误的接线指令可能导致数十万元损失。智能PLC模拟软件创造的“数字沙盒”,则为技术创新提供了安全试验场。在化工行业,某企业通过Linux网关赋能的PLC二次开发平台,将预测性维护算法植入虚拟控制系统,成功将设备故障率降低35%。
更值得关注的是跨协议协同训练的实现。如某汽车制造厂的案例显示,学员在虚拟环境中同时操作西门子S7-1200 PLC、三菱FX系列控制器,通过OPC UA协议实现与MES系统的数据互通。这种打破品牌壁垒的复合型技能训练,在实体设备上几乎不可能实现,却在数字世界打开了工业4.0人才培育的新路径。
3. 智能软件如何塑造未来工业人才的核心竞争力?
2025年某高校的PLC实训报告揭示:使用智能模拟软件的学生,在系统集成能力、编程思维维度等方面比传统组高出2.3倍。软件内置的AI导师功能,可实时分析操作轨迹,针对接线规范、程序冗余等问题生成个性化改进方案。例如在电机拖动实验中,系统能自动识别未接地线等安全隐患,并模拟因此引发的设备宕机后果。
这种“错误-反馈-修正”的闭环训练,正重塑工业人才的培养标准。在博图软件(TIA Portal)的全集成平台中,学员从PLC编程到HMI界面设计的全流程作业,均以可视化数据流呈现,使抽象的控制逻辑变得可触摸、可迭代。某智能制造企业培训主管坦言:“现在的新员工上岗前已完成200+虚拟项目调试,相当于积累了3年现场经验。”
灵动掌控未来!智能PLC模拟软件革新工业自动化实训新境界,这不仅是一场技术工具的升级,更是工业教育范式的重构。对于教育机构,建议分阶段引入虚拟实训体系,初期以基础技能模拟为主,逐步增加数字孪生、AI协同等高级模块;企业则应建立“虚拟-实体”联动的培训机制,将软件中的创新方案快速验证并移植到实际产线;而开发者需持续优化协议兼容性,特别是对TSN(时间敏感网络)、5G工业互联网等新技术的支持。当虚拟与现实的无缝衔接成为常态,工业自动化人才培养才能真正驶入快车道。