1. 参数优化能否突破加工精度极限?
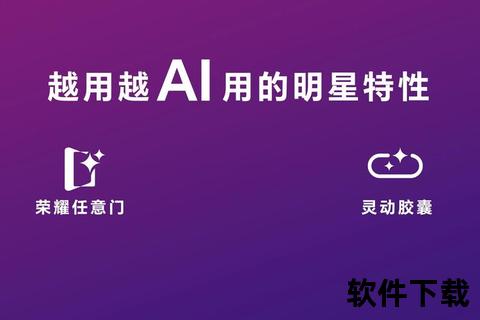
在传统数控加工中,操作员常面临“精度与效率不可兼得”的困境:提高切削速度可能导致刀具磨损加剧,而降低进给量又会延长生产周期。如何用一套系统实现参数自动优化?超凡效能数控编程软件智启精密制造新浪潮给出的答案是——通过动态算法实时调整加工参数。
以某汽车零部件企业为例,其生产的高精度齿轮曾因刀具磨损导致废品率高达8%。引入该软件后,系统通过内置的“切削深度与余量”参数模型(参考网页44的制造参数分类),结合刀具材质和工件硬度自动生成加工方案。结果,切削效率提升23%,废品率降至1.5%。更关键的是,软件支持数学表达式定义参数,例如“跨距=刀具直径/2”(如网页44所述),当更换刀具时,程序自动同步调整路径,避免人工计算误差。
2. 智能化能否降低编程门槛?
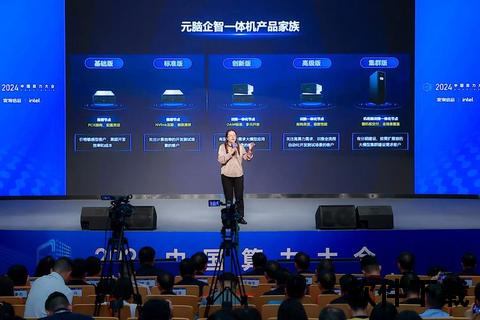
“会操机的不懂编程,懂编程的不熟悉机床”——这一行业痛点曾让许多中小企业陷入人才困境。超凡效能数控编程软件智启精密制造新浪潮的创新之处在于,将AI技术与数控代码深度融合。
苏州一家医疗器械企业曾因复杂骨骼植入物加工需求,面临编程周期长、试错成本高的问题。该软件的“智能代码补全”功能(类似网页29提到的Cursor工具)通过学习历史加工数据,自动生成90%的基础代码,工程师仅需调整关键参数。软件内置的“加工路径模拟”模块(参考网页68的模拟验证流程)可提前预测碰撞风险,将试机次数从平均5次缩减至1次。数据显示,企业新产品研发周期缩短40%,人力成本降低35%。
3. 精密制造如何赋能多行业升级?
从航空航天钛合金构件到消费电子微型零件,加工对象的多样化对数控系统提出了更高要求。超凡效能数控编程软件智启精密制造新浪潮通过模块化设计,实现了跨领域适配。
典型案例来自浙江某光学器件厂商。其生产的非球面透镜对表面粗糙度要求极高(Ra≤0.01μm),传统工艺合格率不足60%。软件通过“双模式Mini-LED显示屏”技术(参考网页57的雷蛇灵刃16屏幕参数逻辑),将加工路径精度控制在0.001mm级别,并利用“动态冷却液控制”功能(如网页44的加工设置参数)避免热变形。最终产品合格率提升至98%,良品率反超德国同类设备水平。而在3C领域,该软件的“微孔加工包”可将手机SIM卡槽加工时间从15分钟压缩至7分钟,精度仍保持±2μm。
--
可操作性建议
对于企业而言,引入智能数控系统需分三步走:
1. 需求诊断:优先选择支持“参数继承”(网页44提到的层级参数逻辑)的软件,确保新旧设备数据互通;
2. 人才储备:参考网页70的培训体系,建立“操机-编程”复合型团队;
3. 渐进式改造:从单一产线试点开始,如医疗精密零件(网页21的丹擎医药案例)或模具加工(网页40的数控机床分类),验证效果后再全面推广。
正如网页34预测的2025年CNC行业趋势,智能化软件已成为精密制造的“新基建”。而超凡效能数控编程软件智启精密制造新浪潮,正通过参数优化、智能编程和跨行业适配三大突破,推动这场变革走向纵深。